By Lewis Kennebrew, Senior Director, Business Process Consulting @ ArcherGrey LLC
Introduction
Many may not be as familiar with the Value Stream Mapping technique as they are with other forms of process mapping. My objective is to introduce you to the technique and to help you understand why and when to apply it.
Value Stream Mapping (“VSM”) is a technique for investigating a business process. The VSM technique focuses on mapping, measuring and then increasing the “value” that the stream of process activities generates. This contrasts with traditional process mapping (“TPM”) where the focus is on accurately describing the process; not necessarily on the effect of that process on what’s valuable to the organization.
Almost everyone in a mature business is familiar with the traditional form of diagraming/mapping a process (i.e. the set of activities and decision points that convert an input into an output). This type of process map may be further enhanced with the inclusion of “swim lanes” which identify which roles are responsible for which steps.
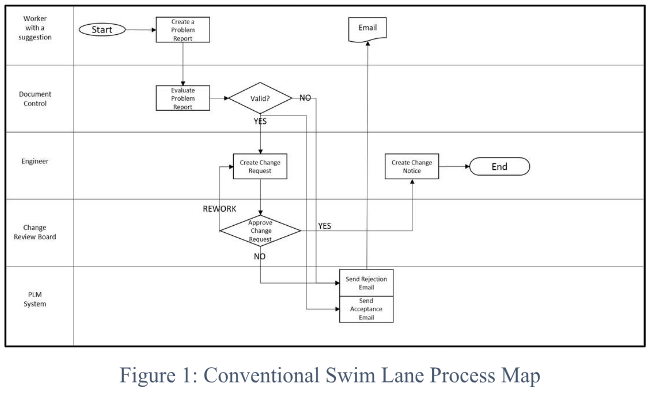
This type of process mapping has its merits and is a mature, proven method for analyzing and communicating the details of a process. VSM is not a substitute for TPM but should be used as a precursor and/or supplement to it. The reason for this is that VSM helps an organization understand “WHY” a process is important and what changes increase the process’ importance. TPM helps an organization understand “WHAT” a process entails. Too often, the focus is on the WHAT before understanding the WHY.
VSM has been used for over a decade in Quality, Six Sigma, Lean Product Development, and Lean Manufacturing disciplines.
For the purposes of this white paper, I will focus on the use of VSM in enabling Product Lifecycle Management (PLM) processes within PLM applications.
I would assert that before any process enablement effort begins within a PLM system, the organization should look at what value and, as importantly, what waste the existing process (i.e. value stream) generates. This is where VSM techniques excel. Once the current-state value stream is understood, a future-state value stream can be created which increases the process’s value to the organization while simultaneously removing waste. This exercise can be done without enabling the future-state value stream in PLM; however, the use of PLM allows a company to automate the process, allowing it to be uniformly applied, consistently used, and automatically measured. Anything that can be measured can be improved, as the saying goes, and PLM affords an organization the ability for continuous improvement through adjustments to the managed processes that are comparably easy to deploy.
How to Improve the Value Stream
Value Stream Mapping (VSM) uses different symbols and operates at a higher level of abstraction than traditional process mapping (TPM). A great book on the use of VSM for product development activities is Value Stream Mapping for Lean Development: A How-To Guide for Streamlining Time to Market by Drew A. Locher. This book provides way more detail and background than what I intend to provide in this brief overview.
Improving a Value Stream is a 4-step process:
- Identify an appropriate value stream to map
- Map the current-state value stream
- Envision the future-state value stream
- Identify improvement areas to target
Step 1: Identify an appropriate value stream to map.
The characteristics you should consider are:
- The subject of the value stream mapping exercise should be a macro-level process that spans from an idealized Customer (preferably an external customer but could be a large internal customer) back through multiple functions within the organization to the idealized Supplier of the first inputs to the process. There are two reasons for selecting this broader scope of project:
- If a Customer cannot observe and appreciate the increase in value created in the future state, then why expend the resources to map and change the value stream? Thus, the objective is to select a process that can have significant positive impact.
- Improvements to processes often involve identifying and mitigating the root causes of waste. If the process does not extend back to the Suppliers to the process, then it would be more difficult to identify and influence all root causes; which would hamper the ability to maximize positive impact
- What components of value should be measured is a major consideration. Many metrics are possible and acceptable if the metrics are easily measurable and affected by changes to the process. The most common metrics investigated during value stream mapping are
- Activity Ratio – the ratio of actual processing time over total waiting (or queue) time. This is a measure of how efficient the process is and the higher the ratio the better.
- First Pass Yield (also known as % Complete & Accurate) – a theoretical measure of what percentage of process inputs make it through the process without any rework necessary. Put slightly differently, how many input items (e.g. documents, change forms) does the process yield in a 100% complete and accurate state in their first pass through the process. First Pass Yield is a measure of process quality.
Process Cost – the labor-related and other measurable costs of the process. This allows cost-based comparisons between the current-state and future-state value streams; which help to quantify the efficiency and quality improvements in the value stream
For step 2: Map the current value stream
Map the current value stream with a cross-functional group of process stakeholders. A value stream map is a more complex and detailed version of another typical diagram called a SIPOC diagram. SIPOC is an acronym for Supplier, Inputs, Process steps, Outputs, and Customer. This provides a great mnemonic reminder of the required components of a value stream map.

- Supplier
- Input
- Process Steps
- Output
- Customer
Additionally, the following components are used to form a more complete understanding of the process:
- Technology blocks
- Data transfer paths (electronic and manual)
- Kaizen bursts
Next, identify the areas where waste occurs and the magnitude of the waste. There are eight waste categories that should be considered:
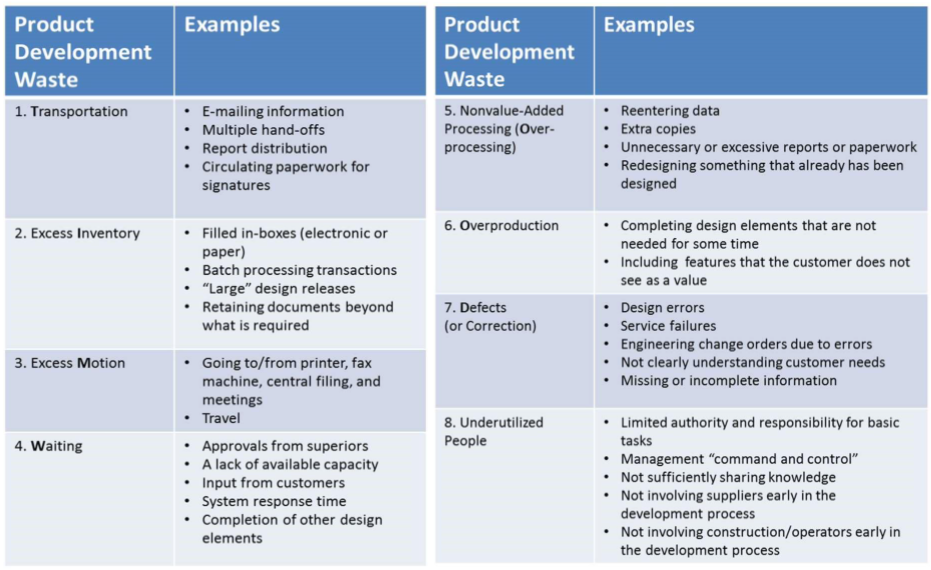
Finally, quantify as much as feasible, the costs of the current-state value stream. This would include the quantification of the previously-selected metrics and the wastes identified.
Steps 1-2, should provide a comprehensive understanding of the Current-State Value Stream.
Step 3: Envision the future-state value stream
First, envision the future-state value stream by first understanding what the top corporate objectives are for the near future. Envision how PLM will help achieve those objectives. This gives you a destination to aim for when developing the future state.
Next, develop an understanding of what is possible in terms of new PLM technology and process changes. Research the latest releases in your existing and competitive PLM technology. Look at unused or under-utilized features of your existing technology. This is where it may be prudent to bring in software vendors and trusted service providers with experience in applying the latest capabilities to solve business needs.
Finally, revisit your current-state value stream, use what you’ve learned about the latest capabilities, and creatively apply those to:
- mitigating the causes of waste identified earlier
- improving each process step
- estimating the new future-state metrics
- comparing the current-state to future state metrics to determine the degree of improvement
Again, involving outside perspectives with experience in this area will increase the amount of improvement you can develop.
Step 4: Identify improvement opportunities
Now that you understand the Current State (i.e. Point A) and can forecast what a Future-State (i.e. Point B) should look like; you need to develop roadmaps for how to navigate from Point A to Point B. This will involve:
- Prioritization of improvement opportunities
- Development of projects to execute those improvement opportunities based on opportunities while considering organizational constraints
- Development of measurement systems to measure the improvement opportunities
This results in a Process Improvement Roadmap that can be implemented and its effects measured against the Future State Value Stream assumptions.
Conclusion
Value Stream Mapping is an extraordinarily powerful tool to affect positive business change that is methodical, inclusive of multiple viewpoints, and easily measurable.
It is an often-overlooked tool in the rush to “get something done”. Before deciding what to do (e.g. traditional process mapping of the “To-Be” process), why not first determine what should be done and what that would be worth?
When it comes to process improvement, it’s better to measure twice and cut once. Value Stream Mapping is a superb process measurement tool, and I highly recommend you consider using it.